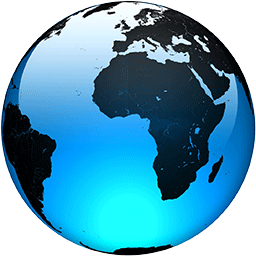
BMW aims to slash factory emissions to offset CO2 of EV production
Electric cars like the BMW iX increase manufacturing carbon footprint by 40%
German firm also targets supply chain as a whole in a bid to reduce overall emissions by 20%
A major operational reset in BMW's factory and supply chain is hunting down huge, 60% savings in CO2 by 2030 to offset rising energy use as the company pushes towards net-zero carbon.
At odds with their capacity to slash carbon output in use, electric car batteries are actually increasing carbon production in manufacturing, because of the heavy energy consumption of the mining/refining process for the rare earth metals used inside the cells.
In fact, BMW's analysis suggests that the switch to battery-electric powertrains for its whole output of 2.5 million cars will increase the manufacturing carbon footprint by 40%, demanding dramatic action throughout the supply chain to maintain progress towards net-zero carbon by 2050.
"Manufacturing of batteries is a significant consumer of energy because of processing the cell materials and is now one quarter of all the CO2 in a battery-electric vehicle," says Thomas Becker, BMW's head of sustainability and mobility.
Each BEV cell, for example, needs multiple major components, a metal or plastic case to contain the liquid lithium electrolyte, rare earth metals like nickel, cobalt and copper for the anode and cathode, and a plastic separator to insulate the anode from the cathode. The bulk of the key materials are sourced from outside Europe and shipped in from Africa, Asia and South America.
As a result, the worldwide switch to an all-BEV fleet will push BMW's manufacturing CO2 up by a whopping 40%, requiring a 60% cut in carbon by 2030, throughout all its operations, to offset the increase and, at the same time, push overall emissions down on the glidepath to net zero.
"We need to bring down our CO2 footprint 60% to get an overall reduction of 20%," says Becker.
Battery cells are already the biggest single contributor to the CO2 embedded in a BEV, ahead of aluminium, which is the biggest contributor in an ICE car.
BMW is committed to a 100% swing towards BEV production, which will be accelerating by 2030 when half of overall group sales go electric, while the company's British brands, Mini and Rolls-Royce, forge ahead with only full-electric cars from the beginning of the 2030s, all feeding through significant increases in battery cell CO2 to the company's carbon footprint.
The major focus of BMW's CO2-reduction strategy is a faster, deeper switch to renewable solar and wind energy for its factories and suppliers, plus more extensive use of "secondary materials" from recycling.
Aluminium, cell materials, steel and plastic are the four main sources of CO2 in the supply chain and manufacturing and Becker says "there is really only one way to decarbonise our plants and manufacturing and that's to look at the heavy energy users and move to green energy".
Aluminium is the highest energy user, with around 10 to 14 tonnes of embedded CO2 per tonne of metal, while steel is a fifth lower, at two to three tonnes of CO2 per tonne of material.
For steel making, the first step is to move from 'grey' energy (coal) to 'green' energy (gas). Another step is electric arc furnaces, but only with a large proportion of recycled material, which melts at the lower temperatures of arc furnaces. Hydrogen-powered furnaces are a longer-term goal.
"We have the four material groups – steel, aluminium, the cell material and plastic – and for all these you have two pathways for taking carbon out," says Becker.
"One is to replace grey energy with green energy. That's easy if you talk about electricity, but much harder when you talk about the steel industry, replacing blast furnaces by electric arc furnaces.
"The second option is to replace primary material by secondary material. So you have eight different pathways."
BMW says it has already entered into 400 contracts with suppliers who use 100% green energy. A specific example is alloy wheels for BMW and Mini models, which will only be produced with green electricity from 2024.
Also new is a supply of aluminium smelted using solely solar power in the United Arab Emirates, operational from February last year.
Together with corporate responsibility clauses, BMW is moving to a point where it will only sign supplier contracts with companies that comply with its green requirements.
Recognising the difficulty of chasing carbon out of the supply chain, which is made up of thousands of large, medium and small companies, BMW is tasking its own manufacturing plants with the largest of the savings - 80% by 2030 - while supplier burdens will be 20%, both compared with 2019 figures.
Other energy consumers in factory operations – such as the production line, welding machines, lighting and heating – will need to be addressed but are much smaller CO2 contributors in comparison with the four major sources.
"We have set ourselves the goal of building the most sustainable supply chain in the entire automotive industry," says Becker.
It might not be as exciting as the effort to win a Formula 1 world championship or llft the winner's trophy at Le Mans, but BMW is embarking on its most significant challenge yet.
*All BMW’s retired prototypes go through the RDZ facility to have all recyclables extracted*
In a factory unit in the Munich suburb of Lohhof, BMW is perfecting the age-old art of dismantling cars. Given the grimy nature of the RDZ (Recycling and Dismantling Centre) building and the primeval clanking of mechanical diggers, it's hard to see this as the cutting edge in the fight to keep global warming to 1.5deg C.
But BMW is very proud of this facility, which it claims as the biggest in Germany, having capacity for 10,000 cars a year, and an annual haul of 13,000 tonnes of recycled material.
All BMW's retired prototypes go through here and there's even an i8 headed to the car graveyard on our visit.
The monetary rewards are scrap metal prices in the thousands of euros. A tonne of copper can fetch up to €8000 (£6680), aluminium €1000 (£835).
But the rewards are more than monetary. "If I can reuse the engine, that's the biggest saving we can make," says Steffen Aumann, head of the RDZ.
It takes about four man-hours to dismantle a car and the process literally goes off with a bang as the first operation neutralises every airbag in a series of impressive controlled detonations.
Fluids are drained, while headlights, doors, bonnets and engine/gearbox modules are removed for resale.
The surviving carcass is then picked over by a tracked digger equipped with narrow hydraulic jaws specially designed by BMW.
Incredibly, the operator is able to extract the dashboard and wring loom in one piece by spinning the jaws as if winding spaghetti around a fork.
Recovering key materials like copper and alloy from components is handed over to specialist 'shredder' companies, who chop the car into small bits and use sorting technology to recover the small pieces ahead of smelting back into 'secondary' material that feeds BMW's production lines once again.
*Thomas Becker on the design of the sustainable car of the future*
How will car design and engineering change as sustainability becomes more important?
"The entire logic of how to design a car for sustainability is a different story."
In what way?
"For the ICE car, it is all about saving CO2 at the pump, but if you talk about saving CO2 in the making, you really have to have a completely different calculation logic."
How does that filter through to the cars themselves?
"For combustion-engined cars, it is all about weight-saving, meaning less combustion on the road. So we had this big competition for lightweight, like aluminium, composite and high-strength steel."
Is that different for BEVs?
"If you look at a car that has much less CO2 in the use phase, but much higher CO2 footprint in the making, like a BEV, the relative position of steel versus aluminium changes, because the savings need to be in manufacturing."
And in design terms?
"The advantage of composite material shrinks a great deal and weight becomes less important. And if you look at components in the car, there is a case to accept heavier designs, like seats, where the priority becomes easier to dissemble, easier to separate materials and easier to recycle."
Is that something you are working on?
"We are investing heavily in the expertise and we have dedicated people whose job is to redefine these design optimisation criteria."
What about costs in design and manufacture?
"As we learn more about the detail of exactly where the CO2 is in our business, the volume of CO2 you can reduce with every euro spent doesn't remain constant, so that means our purchasing and product development guys need permanently to check how much CO2 savings do I get for each euro spent."