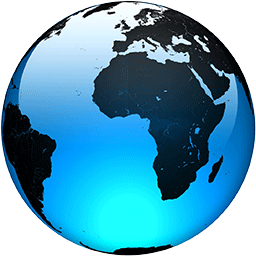
Millbrook operator's new Morocco test centre cuts R&D costs in half
The fundamental business case for the MMAC is centred on low-cost operations
African site will become important year-round proving ground due to reliable dry weather
A new 1200-acre vehicle proving ground has opened in North Africa with a unique low-cost operating structure that is claimed to save car makers between 30% and 50% on new car testing costs.
The Morocco Mobility and Automotive Centre (MMAC) is a joint venture between AngloFrench testing facility operator UTAC and German engineering consultancy FEV.
They believe it will become an important year-round automotive testing hub, taking advantage of reliable dry weather and low operating costs while being located conveniently close to major manufacturers’ technical centres in Europe.
“We can see a bright future for our Moroccan site, because it offers several advantages: [lower] costs and a high level of education and socioeconomic environment at a time when [manufacturers] are always looking at operating more efficiently,” said UTAC chairman Laurent Benoit.
The site joins four existing European UTAC facilities, at Millbrook in the UK, Montlhéry and Mortefontaine in France and Ivalo in Finland.
Carved out of a former phosphate mine outside the city of Oued Zem, some 100 miles south-east of Casablanca, the MMAC features 18.6 miles of test track and eight workshops and emissions labs.
UTAC has an operating lease of 25 years on the site from the Moroccan government, which paid the construction costs for the tracks, buildings and infrastructure.
The fundamental business case for the MMAC is centred on low-cost operations. This guided the design and layout of the 14 test tracks, including the main 2.6-mile, 12-metre-wide high-speed track, configured in a triangle, with three straights connected by long-radius corners of 450m, 500m and 550m, for endurance testing of volume-production cars rather than extreme-speed running of supercars.
This track allows a maximum “stabilised” speed of 100mph, although higher speeds are possible by negotiation, and the maximum incline is 12%, giving it some elevation.
*The site as seen by satellite*
Use of the MMAC is flexible and can be tailored to all aspects of a testing and development programme, but UTAC sees the initial demand being focused on endurance and durability testing, with labour-intensive portions of engineering programmes for internal combustion powertrains and electric vehicle components, which involve multiple shifts of repetitive test track driving to put components under real-world strain.
Also among the 14 test tracks at the MMAC are a sinuous multi-corner road circuit 2.9 miles long and seven metres wide, featuring copies of some of Europe’s best driving corners; and a 2.5-mile coastdown track, constructed over 12 months to a close-tolerance specification, including a precise gradient of 0.7%.
An important new engineering asset for the European car industry, the coastdown track is used to gather real-world ‘road load’ data for calculating current Euro 6 and forthcoming Euro 7 fuel economy and CO2 emissions figures.
Other testing facilities at the MMAC include a lowfriction wet/dry pad for brake testing with a split coefficient of friction option; an urban track for simulating frequent stop-start motoring; and a car-breaking zone with Belgian pavé, extreme bumps, water splashes and corrugations to simulate desert driving.
UTAC won’t be replicating high-investment testing labs such as Millbrook’s battery testing facility, though. “We don’t need a second site for that,” said Benoit. “If we have more demand for battery testing, we will expand Millbrook. It doesn’t make sense to duplicate.”
Of course, much of a vehicle’s development and testing is carried out in laboratories and workshops, and so the MMAC has facilities dedicated to UTAC contract activities, powertrain developer FEV and clients such as car-making giant Stellantis, which has taken a workshop. Other manufacturers are expected to join them.
Stellantis, whose CEO Carlos Tavares is renowned for his focus on reducing costs, already has durability testing under way at the MMC. The site is conveniently located for its factory at Kenitra, near Rabat, which makes the Citroën Ami and Peugeot 208.
UTAC’s own workshops are supporting contract work for manufacturers, which might include high-labour content testing. An example of this is static wear testing of trim and components like door hinges, which are put through repeated open-close operations, with a test operative also entering and exiting the passenger seat to subject trim and upholstery seams to real-world wear.
Costs for a test programme like this might be reduced by 50%, thanks to the lower labour costs in Morocco. FEV has a large test lab at the site with nine functional areas, each kitted out with test rigs, including a chassis dynamometer, an ICE testing lab and a heat-soak room with temperature boxes that can cool or heat a car from –20deg C up to 50deg C.
“Repeated heating and cooling cycles are used to accelerate wear and degradation testing,” said UTAC durability testing head Philippe Artous.
*"Better business case" than building new Nardo*
“We talked to potential clients about their needs and had demand from premium car makers for a very high speed circuit, but the cost for building this type of track would have doubled the cost of the whole [MMAC] facility,” said Benoit.
The demand exists for a second high-speed track near Europe to complement the 7.8-mile circular track in Nardò, Italy, where sustained high speed running at near 200mph is the key offering, because track time there is notoriously difficult to book.
And future demand ought to be even higher, as there are, for example, around a dozen electric hypercars in development, with propulsion outputs of 1000bhp and top speeds in excess of 200mph, and each will need to undergo extensive high-speed testing.
But UTAC needed a 10-year commitment from clients to justify investment in a Nardò rival, with estimated build costs of around £43 million, and that commitment wasn’t forthcoming.
“We had a better business case and demand from clients looking for a test centre with a low-cost operating base, so that was the direction we decided to go,” said Benoit.