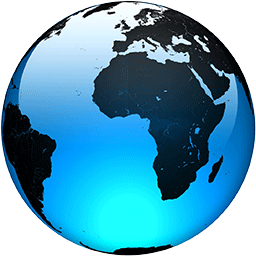
If you can think it, they can make it: meeting Envisage Group
We visit the world leader in creating concept cars, coachbuilt one-offs and low-volume specials - even for big car firms
You might not have heard of the Envisage Group – but you’ve almost certainly seen some of its work. Envisage has been responsible for the design, engineering and production of everything from gleaming motor show concepts and production-previewing prototypes to comprehensively re-engineered road-legal cars and one-off bespoke creations. They just might not be able to tell you about it.
The firm – established in 2009 and now encompassing four distinct divisions, four sites in Coventry and two international offices, in India and the US – has quietly grown into an industry leader in the expanding market of coachbuilding: creating limited-volume cars, either through the use of a bespoke platform or extensively reworking a donor vehicle.
Although a large stack of non-disclosure agreements prevents Envisage from revealing many of the projects it has worked on, they include static motor show concepts for major car firms – also known as OEMs within the industry – and a working pre-production prototype of a future electric supercar. Other assignments encompass production and engineering commissions for smaller design firms, and one-off or limited-run projects for enthusiasts who simply want to design their own dream car. Given the inexorable rise of coachbuilding in the car industry, Autocar asked Envisage to talk us through the process of turning a loose idea into a fully fledged machine.
*The starting point*
By definition, no two coachbuild projects are the same, with huge variance in timescale, budget, ambitions and expectations. So the first task is to work out the starting point and the expected outcome in order to understand the scope of work involved in the project.
Those starting points can range from a true blank sheet of paper to a complete design that a car maker needs turning into a proof-of-concept one-off working show car.
Designs will generally start with sketching out rough ideas or producing mood boards – collages of pictures that hint at the desired style and themes of the vehicle. Those designs are then refined using digital rendering software. Even with a blank-sheet-of-paper design, there will be some constraints in the form of hard points – set design elements for engineering, safety and so on.
“We’ve got different aspects to the business, from pure coachbuild to working out how to build a concept vehicle for a client, or turning a full design into a working concept,” says Envisage CEO Tim Strafford. “If it’s pure coachbuild, a client will come to us with an idea, and we’ll work with them to create a sketch. That will then go to our design team to start working on renderings.”
The next level up is perhaps the truest distillation of coachbuild projects: where a client wants a bespoke car based on the underpinnings of an existing one. Then there are assignments where Envisage is essentially given an existing design, usually in the form of digital CAD data. “We’re often tasked with making show cars for clients, and so for those we won’t do the full design: that will be done by the OEM and our job will be to turn that into a one-off concept,” says Strafford.
Even at this stage, whether the car has to be road legal is a key consideration: if it does, Envisage’s designers will have to make certain the bodywork styling is legal, ensure the lights are in the correct place, account for crash structures and so on.
*Engineering and underpinnings*
To speed up the process, Envisage operates a parallel working method: rather than wait for the designers to finalise the styling of a vehicle with the clients, the firm’s engineering arm will immediately start work on its underpinnings.
That process requires the two teams to work closely to stay in sync, but it also greatly reduces the lead time for projects – a key step when some of Envisage’s work, particularly show cars, is done in incredibly short order. “The engineering team will also work directly with the clients at the same time as the designers, and it’s absolutely key that they really understand the requirements the client has for a car,” says Mick Bradley, Envisage’s production director. “The engineers need to fully understand what the car is required to do. They will then create an engineering-based proposal, which builds in the work of the design team. After that, work can begin on a clay model.”
The complexity of the engineering job will depend on both a client’s ideas and whether the outcome is a rolling chassis, one-off or road-legal low-volume production run.
Exactly how much engineering will be involved also has an impact on what the project will be based on, particularly in the case of design-led coachbuild jobs. “We need to understand what the base vehicle might be,” says Bradley. “Sometimes clients will want a specific donor car to be used and sometimes we can work with them to find something that best fits the project.”
Bradley explains that there are a range of road cars the firm has experience of working on and that it will suggest to clients if the project fits. Those will be machines that Envisage knows how to engineer and, in some cases, it has a relationship with the vehicle’s maker and can gain access to CAD data, which can accelerate the project.
An example of that is the engineering work Envisage did for a reimagined classic-inspired sports car. After completing a series of studies to ensure the desired bodywork could be overlaid onto a modern donor car and still be road legal, Envisage sourced CAD data from the manufacturer to back up its findings and further refine the design.
Much like the design stage, the intended use of the vehicle will heavily influence the level of engineering required, particularly in terms of the drivetrain. “A lot depends on what the finished machine needs to do,” says Bradley. “If it’s a show car or low-speed concept, the engineering needs are very different from something that has to be road legal.”
Envisage has its own low-voltage vehicle platform, which it has extensive experience of using and which, Strafford says, “enables us to offer a complete engineering package that we can make rapid progress on projects with”. That flexible platform will generally be used for show vehicles, which are likely to need to be driven only short distances at slow speeds.
For OEM projects, Strafford says Envisage will often be required to build a show car based on the car maker’s own platform. “Sometimes a manufacturer will use a concept car to either test their structure or showcase the technology it offers, so we’ll have to use that,” says Bradley.
*The Approval process*
Depending on their interest and desires, the client will often be involved throughout the design and engineering process. But there is still a final sign-off at the end of this phase, and that comes when the design and engineering work is integrated into a full technical concept. “The technical concept will be very comprehensive and include every aspect of the design, the full product specifications and even vehicle benchmarking data for comparison,” says Strafford.
Keeping the client happy is a key part of the coachbuild process and Envisage has invested in 3D virtual reality visualisation software to give them a true impression of what the final car will look like. The data can be fed into the system, with light, shadow, paint and other details added. Envisage also uses physical clay models and can even build show cars and prototypes if needed.
Strafford says that clients rarely demand big changes at the final approval stage. “Because we work with them throughout the process, there shouldn’t be any big surprises,” he says. “We also work at every stage to make sure they understand what is possible within their budgets and any technical and legal constraints.”
*The production process*
The technical concept Envisage has produced effectively acts as a set of blueprints, and once signed off, the project can proceed to the manufacturing phase. Depending on the project, this can take many forms: a one-off car, a very limited-run model, a series of conversions or more.
Envisage can go a step further than many automotive design consultancies thanks to its in-house engineering arm, Envisage Technologies, which can create anything from clay sculptures, models and prototypes to full low-volume production runs.
“It really sets us apart,” says Craig Bonham, Envisage’s chief engineer. “Being able to link the design and manufacturing is a key strength. Our design team know exactly what our engineers are capable of and we’ve got vast amounts of experience in-house.”
Envisage Technologies has a range of five-axis and other CNC machines, and has also invested heavily in 3D printing technology to reduce lead times – particularly useful when working on OEM show cars, which are often required at very short notice. The team also has to produce tooling moulds and has an in-house colour, materials and finish team.
It’s not just new cars, either: the firm’s Classic and Bespoke division specialises in the sort of hand-crafting work required for restoring and maintaining classic cars. Many of those skills are also transferable to the other assignments the firm is working on, which is especially handy for coachbuild projects based on existing machines. Envisage can handle low-volume manufacturing, of vehicles of any given design, in-house.
*The finished product*
Whether it’s a one-off show car or a low-volume coachbuild project based on an existing road car, Envisage’s goal is to realise – as much as is possible – the machine outlined by the client in that initial design chat. “Coachbuild is all about giving the client what they want,” says Strafford.
“That’s our goal. Within reason, we can deliver anything that a client wants – so that when they take delivery of the machine, it’s exactly what they had hoped for.”
*Here are four they made earlier*
Professional discretion and non-disclosure agreements mean Envisage won’t actually talk about projects it has worked on. But here are some we have learned of that they played a role in.
*David Brown Speedback GT (2014):* This is a true coachbuild project: taking the chassis of a Jaguar XKR and adding a bespoke chassis that draws inspiration from classic 1960s GT cars such as the Aston Martin DB5. The chassis is made from hand-formed aluminium panels. Envisage built the prototype model for the car’s 2014 launch and then produced the bodies for the low-volume production run.
*Bentley Continental GT Zagato (2012):* Fabled Italian design house Zagato produced a run of nine coachbuilt Continental GTs. Each 200mph-plus car cost more than £500,000 and was heavily reworked from the Bentley original, shedding more than 100kg through a bespoke body. Envisage worked with Zagato to create the hand-crafted bodies, which feature Zagato’s ‘double bubble’ roof.
*Jaguar D-Type Continuation (2018):* Jaguar Land Rover Classic’s third continuation vehicle – after the E-Type and XKSS – was a recreation of the machine that won Le Mans three times between 1955 and 1957. Envisage’s classic arm was reportedly involved in the project by hand-crafting the bodies using traditional methods to JLR Classic’s precise specifications. Several of Envisage’s team had previously worked for the firm.
*Bentley Blower continuation (2020):* Bentley’s Mulliner division will produce 12 recreation versions of the famous 1929 4.5-litre Blower, each costing around £1.5 million. The project involved stripping down Bentley’s original Blower to catalogue, capture and recreate every single part. That project was based at Envisage’s base in Coventry and used the firm’s high-tech measuring tools.
*READ MORE *
*Mulling things over: What next for Bentley coachbuilding division?*
*Better off alone: How Niels van Roij carved his own path*
*Back by popular demand: reinventing the Ford Capri*